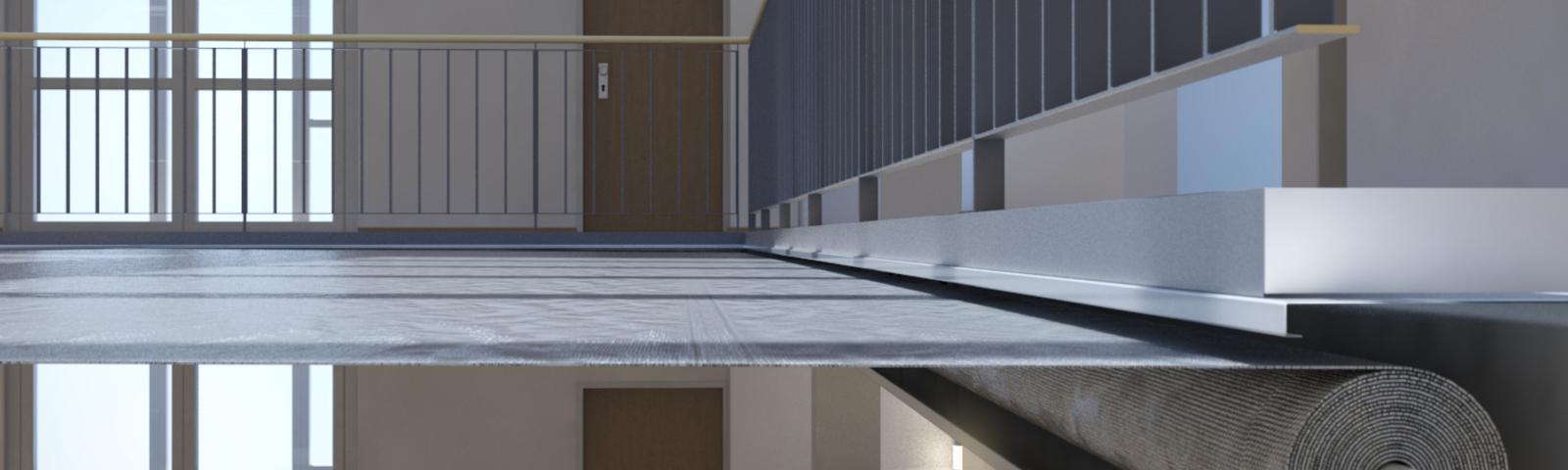
Good material!
Performance capability of fire protection curtains
For many architects, textile fire protection curtains are an aesthetic alternative to fire protection doors, gates or dampers. These curtain systems are also seen as a great solution when space is tight or if there are large openings, which is why they are growing in popularity among planners.
Along with the well-known fire protection doors, gates and dampers (see DIN 4102-5), another type of fire protection solution is increasingly establishing itself: textile fire protection curtains. These are becoming increasingly attractive for planners and architects and are regarded as a sophisticated alternative in terms of creativity to the conventional massive closures mentioned before. But what do these systems provide and what are their benefits? What are high-tech fabrics and can they be issued with a proof of usability?
Structure and functional principle
A vertically closing textile fire protection curtain (standard model) functions similarly to a Venetian blind. It basically comprises the following components: casing design, lateral guide rails and the textile surface including the closing strip. The steel plate casing houses a winding tube with an internal drive (tubular motor). The casing box serves to hold the winder on which the fabric is wound up and stored. Depending on the size of the system, the winder has fixed or floating bearings. Depending on the design of the curtain system and the type of textile used, today’s fire protection curtains fulfil the European classification acc. to DIN EN 13501-2 [3] , the performance criteria E (room closure), I (Insulation) or W (restriction of radiation penetration). Also, thanks to their classified properties with respect to fire resistance behaviour, these systems comply with the requirements of the official building approval-related usage regulations (flame retardant, highly flame resistant etc.).
In the event of a fire, the fabric is unwound and the wall opening is closed. The lateral guide rails guide the curtain down to the floor during closing and also keep the curtain in position even, at high pressure under fire load. A closing element at the lower end of the fabric surface (closing strip) connects the curtain to the floor. One condition for operating both conventional fire protection closures and also textile fire protection curtains is that they are ‘self-closing’. In the case of automatic fire protection curtains, this means that they always need to be equipped with a brake control system approved for fire protection closures. The curtain is kept open by an on-site power supply until fire detection elements (e.g. smoke or heat sensors) send a fire alarm signal to the control system and triggers the closing process. The system is closed in speed-controlled manner by means of a gravity-supported Gravigen unit. The well-known problem of wedged-open fire doors that do not have a hold-open device is not something associated with curtain systems, however they cannot be used in rescue routes.
Performance capability
When looking at a fabric that is only 1 mm thick, most people find it difficult to believe that it is able to withstand fires in the same way as solid closures like gates or doors. However, modern textiles are easily able to withstand temperatures in excess of 1000°C verifiably for several hours. Also, these kinds of curtain systems with the right fabric structure can even reduce radiation by approx. 90%. This is especially interesting for the frequently discussed use of textile systems in escape route areas.
There is a lot of development effort that goes into the production of these high-tech fabrics including complex weaving, coating and lamination techniques. The result of modern production procedures are highly durable composite surfaces made of fabrics, metallic or plastic films. These kinds of curtains not only have high fire resistance qualities, they can also reduce the previously mentioned radiation penetration (EW-classification).
The enormous capability of an aluminium-coated glass filament cloth for the limitation of radiation can be explained in simple terms as follows: In case of fire, the heat input into the textile on the side facing the fire is largely due to thermal radiation and significantly less due to convection (convective flow of heat).
The integrated aluminium coating now reduces most of the heat radiation into the fabric to a minimum.
The coating also has another function. It prevents the emission of infrared heat radiation on the side facing away from the fire. Also, very thin silicone films react to the impact of the temperature and, in combination with the various materials, form a highly temperature resistant coat. The complex structure of the fabric also minimises the thermal conductivity profile and, at the same time, improves the thermal resistance. As a consequence, the insulation effect is highly effective.
The radiation limitation method is only surpassed by thermally insulating curtain systems. Their structure however differs from the described standard structure because they not only comprise a rolled-up fabric element but also clever multi-chamber ventilation equipment.
System diversity
Fire protection should function but not be conspicuous! And even if conventional doors and gate are increasingly able to satisfy growing demands in terms of aesthetic standards, they still impact on the building design as a result of their structure. Textile fire protection curtain in particular have proven to be an extremely flexible fire protection solution, especially for very open and transparent building design concepts. The focus here lies on three important aspects: the closure of very large wall and ceiling openings, their almost invisible installation and the great design freedom afforded to the architects and planners. Textile fire protection curtains (rolling technique) do not intervene in the room concept, they can be installed very flexibly in a number of system designs. The frequently very small casings can be mounted either on the wall, under the ceiling or completely in intermediate ceilings. The necessary guide rails can either be mounted visibly on the wall or 'invisibly' in the embrasure. This achieves the best possible fire protection shield without limiting the room concept.
At the end of the day...
As far as the design is concerned, fire protection curtains are very versatile. Their greatest advantage is their almost invisible integration into attractive high-quality and open architectural concepts. An important technical advantage is of course their low weight which means a smaller load on the building structure, smaller casing dimensions and impressive system sizes. With respect to the proof of usability for textile fire protection curtains, it is expected that the coming product standard DIN EN 16034 will make things easier for all parties and not just the manufacturers of building-related fire protection products.